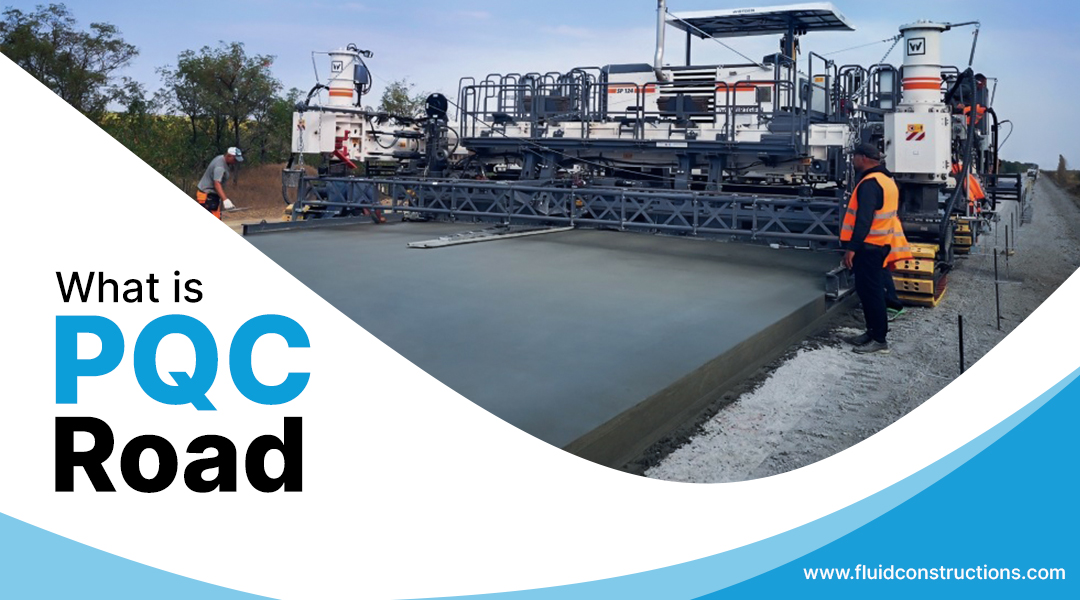
What is PQC Road
Concrete roads, despite their high initial cost, stand out due to their extra sturdiness and extra long life without the need for maintenance. In concrete roads, although mostly made of PCC (plain cement concrete), PQC roads are becoming more commonplace as an enhancement with their even superior strength and durability.
PQC in road construction
All hard-surfaced roads are divided into two categories – flexible pavements and rigid pavements. Their difference mainly lies in the types of surface layers. The surface layers of flexible pavements are made of bituminous concrete (asphalt), whereas rigid pavements are made of cement concrete.
Pavement Quality Concrete or PQC is a special-purpose cement concrete used for building the top layers of rigid pavements because of the following advantages:
- High strength so as to distribute the wheel load of the vehicles to the bottom layer’s without any deformation.
- Resistance to abrasion caused by the tyres.
- Should minimize the skidding of vehicles.
To achieve the above the concrete should be strong, hard and durable. Thus PQC is a special grade of Concrete suitable for highway construction.
PQC (Pavement Quality Concrete) roads use reinforcement bars to withstand more wheel loads from large and heavy traffic. This makes PQC a better choice for the surface layers, laid over the PCC sub-base course in the construction of expressways and runways in airports.
The conventional normal grades of concrete are not technically suitable for preparing PQC and hence it is recommended to develop M30 grade and more to achieve the requirements of PCQ.
PQC road construction
A PQC road structure consists of a base course and a surface course. As said earlier, the surface course is made of a PQC layer of 300 mm thickness, laid over a DLC (Dry Lean Concrete) base course.
PQC Road Materials:
The below list comprises the essential materials for PQC construction:
- Coarse aggregate of 20mm size particles
- Fine aggregates of 10 m aggregate size
- Sand with crushed stone dust
- OPC Grade 43
- Admixtures
- 32 mm diameter dowel bar
- 12 mm diameter tie bar
- Poly Sulphide sealant
- Epoxy
- Anchorage grouting compound
- Curing agent
- Membrane of a given thickness for separation
Detailed specification of the materials:
Cement:
The cement used is Portland cement of grade 53 only, mixed with fly ash up to 20%, GGBFS (Ground Granulated Blast Furnace Slag) conforming to IS:12089, and OPC content at a blending ratio of 310 kg./cum as per IRC:44. If Portland Pozzolana cement is used, the fly ash content should be not more than 25%. The cement must be sulphate resistant and of IS:12330 standard.
Chemical admixtures:
Adding the admixture improves the workability of the concrete or extends the setting time without affecting concrete strengths, volume changes, and durability, and does not affect steel bars negatively. For PQC road construction, the admixtures used should conform to IS:9103 and IS:6925.
Fibers:
Depending on the designer’s approval, steel (IRC SP:46) or polymeric synthetic fibers can be used to reduce shrinkage cracking and post-cracking. The fibres used shall comply to MoRTH Section 600, clause 602.2.3.1.
Coarse aggregates:
The aggregates used in PQC construction work shall comply with IS:383 and have a Los Angeles Abrasion value of not more than 35%. The amount of deleterious materials allowed should be based on table 600-2 from MoRTH.
The maximum size of coarse aggregate shall not exceed 31.5mm. Water absorption should not be more than 2%.
Fine aggregates: According to IS:383, the fine aggregates for PQC building work might be crushed stone dust, clean natural sand, or a combination of the two. Clay, shale, loam, cemented particles, mica, soft particles, and other foreign matter should be absent. Before designing the mix, it is crucial to determine the amount of mica present in the fine aggregate and to account appropriately for the potential loss of strength in the concrete.
Water:
Water quality should be as per IS:456 i.e. pure and free of contaminants such as hazardous oil, salt, acid, vegetable matter, and other materials.
Mild steel bars for tie bars and dowels:
Typically, they are just plain bars that are occasionally taped, lubricated, or inserted into snug-fitting sleeves on one end. There are proprietary substitutes.
Tie bars offer coherence in every direction. They are frequently distorted bars that are positioned over the joint of two nearby slabs. In roadways, they are typically positioned across longitudinal joints, with keyed joints frequently.
MS bars should match IS:432, which specifies a dowel bar with a yield stress of Fe-240 be made of plain mild steel. Tiebars are made of TMT steel and according to IS:1786 is required when it has a yield stress of Fe-500.
Construction procedure
- There should be a seven-day break after the PCC base course or DLC is laid, before overlaying OF PQC. Dowel bars measuring 32 mm in diameter and 500 mm in length must be installed in accordance with MoRTH clause 602.6.5 and kept at a distance of 220 mm between centres, or as per the authorized pavement design.
- A 640mm-long tie bar with a diameter of 12mm must be positioned at a center-to-center distance of 550mm in accordance with paragraph 602.6.6/Approved pavement design. Side formwork must be built true to the line and level before PQC is placed.
- Separation membrane (impermeable and transparent) or white PVC sheet ( 125 microns thick) spread flat over DLC with as few wrinkles as possible in accordance with MoRTH clause 602.5, prior to PQC.
- PQC mix will be transported to the location after being prepared in a fixed automated batching facility. Either a human placement or an automated paver will be required. In the event that the mix is laid manually, it must be fully compressed using a needle vibrator and a screed vibrator.
- Strict quality control must be carried out on the PQC laid, following MoRTH regulation 903.5.2.1. The plant will mold the beams for flexural strength and the cubes for compressive strength, and the site lab will test them at a predetermined period.
- The compacted surface of PQC must have the texture as per MoRTH paragraph 602.9.8. After three hours of PQC laying, the textured surface must be sprayed with the approved curing compound in accordance with MoRTH clause 602.9.9. For 14 days, it should be maintained moist and covered suitably with a damp hessian cloth.
Different types of joints and their laying
Rigid pavement roads have joints to prevent cracking from temperature fluctuations, shrinkage, and other causes. There are 3 types of joints
Contraction joints
Transverse contraction joints with dowel bars must be installed at the predetermined places indicated in the construction drawing. Contraction joints need to be 3 to 5 mm broad and 1/3rd to 1/4th of the slab’s depth, plus or minus 5 mm, as indicated by the drawings.
Widening the contraction joint to accept the sealant as per IRC:57 or Clause 602.11 is required.
Expansion joints
To prevent any form of expansion cracks, expansion joints must be installed in the PQC slab at predetermined intervals. Every expansion joint must have a joint filler board. Expansion joints of at least 25 mm in width and half the pavement’s depth must be installed after the necessary length of concrete (as specified in the technical specifications or plan).
Longitudinal joints
A longitudinal joint that connects two lanes. Tie bars will be installed throughout the venue. Tie bars do not transfer loads. After saw cutting, longitudinal joints must be
made as per IRC:57’s dimensions. After the last set of PQC, the groove can be created with the aid of a cutting machine.
Tie bars must be installed at each longitudinal joint according to clause 602.6.6.6, keeping the dimensions and spacing specified in the construction drawing.
Concreting procedure
The pavement must be laid with PQC of at least M-35 grade. Concrete shall not be laid
until all necessary preparations, including crack prevention and curing mechanisms, have been made. In windy or rainy weather, concrete must be differentiated.
Every pour must have the necessary protective covers and spreading mechanism without damaging the texture. Concrete slump shall be limited to 50mm, and placing shall begin at one end.
Using wooden screeds, distribute the concrete uniformly and rough level it. Surface-mounted vibrators will be used to vibrate the leveled concrete and polish it to a rough texture, and the slump value should be 15 to 45mm.
Curing
Curing of completed pavement must begin immediately following the final setting of concrete. The initial curing will be accomplished by covering the surface with wet hessian, followed by ponding.
Sealing of joints
Every expansion and construction junction must be sealed with IS-1834 Grade-A bitumen sealant.
Conclusion
Concrete roads, though initially costly, stand out for their durability. Pavement Quality Concrete (PQC) enhances strength, making it ideal for highways. Material precision, reinforcement bars, and stringent quality control define PQC construction. The process involves a base course, PQC layer, and meticulous joint sealing. This approach ensures longevity and performance, marking a commitment to resilient infrastructure.